Introduction
With multiple North American manufacturing sites, companies are capable of providing robust, repetitive and redundant manufacturing processes and capabilities. The recent national pandemic and on-going inclement weather issues validate the need for companies to have multiple manufacturing sites. This guarantees reliability for the manufacturing of products.
Understanding the Value
In engineering, redundancy is the duplication of critical components or functions of a system with the intention of increasing reliability of the system, usually in the form of a backup or fail-safe. This principle can also be applied to manufacturing processes and facilities.
The majority of EaglePicher’s nine North American locations are established in the Midwest. This part of the country witnesses more inclement weather than other areas. The area is susceptible to extreme high heat in the summer, cold wind chills with ice and snow in the winter, flooding in the spring and is in the country’s tornado alley. Due to this, it is necessary for EaglePicher and our customers to consider the use of redundant, qualified facilities to manufacture any and all batteries.
In recent history, there has been severe and unexpected situations that stopped production in the immediate area of a single facility. Having the ability to utilize redundant facilities to produce the same batteries is a major risk mitigation for all parties. This process allows for production to continue with little to no interruptions to customers’ supply of batteries.
Understanding the Process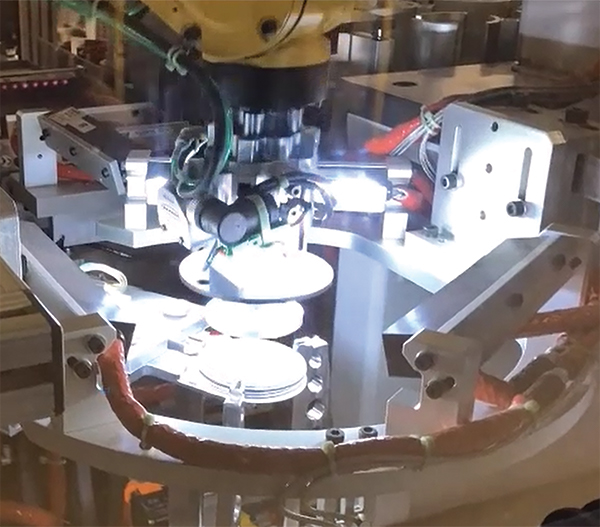
EaglePicher facilities located in Joplin, Missouri and Pittsburg, Kansas manufacture many of the same products and utilize the same overall processes. Both the Joplin and Pittsburg facilities are able to manufacture high quality thermal batteries to meet or exceed even the strictest application requirements. Drawings, processes and tooling are shared between both locations to manufacture the exact same thermal batteries. Most equipment utilized in the production process is the same at both facilities. The Pittsburg facility is qualified to build twelve different thermal battery designs at any given moment. Over the last two years, the Pittsburg facility has built an average of 9000 batteries per month.
A key component of a thermal battery is the powder. Both facilities utilize the same powder during production ensuring battery consistency. The header assembly is at the beginning of the battery assembling process. Both facilities utilize the same machinery, processes and quality assurance for this assembly.
The Pittsburg facility was established in 2005, and utilizes more automated equipment than its counterpart in Joplin. The press room is where some differences start to appear. In Pittsburg, servo presses are utilized with automated quality checks integrated into the system. This is accomplished through the use of cameras, scales and automated thickness checks, all employing robotic transfers. The operator’s role is to keep powder loaded into the machine and provide visual inspection of the final product before sending it to the next operation. The stacking of the battery in the assembly room is also automated.
The battery stacking machine utilizes robotic transfer of the pill chemistries through camera checks. This specialized checking process ensures the correct sequencing and pill integrity. A programmable logic controller (PLC) regulates sequencing and the cameras monitor for foreign object debris (FOD) and cracks before placing pills on the stack. Once the stack is completed, at either location, the local operator wraps the battery in the same fashion.
In Pittsburg, the equipment utilized to weld the battery is also automated. The equipment uses servo presses and servo spindles to present the battery to the weld torch. The weld torch itself is driven by sensors built into the system to control the arc length and distance from the battery.
Once the battery is welded at either facility, it goes through the same quality checks. All of the same equipment and processes are shared between the two facilities to ensure the batteries match the prints and other standards prior to shipping.
Summary
With redundant manufacturing sites, EaglePicher enables customers to confidently sole source, trusting that regardless of the equipment or facility failure, or local disaster, an uninterrupted supply of high-quality products can be manufactured. Our knowledgeable and experienced labor force operates under and shares best practice processes throughout multiple locations to provide customers with quality solutions. Each facility has implemented the same quality system, ensuring the demands of the mission-critical applications we serve are met without interruption.